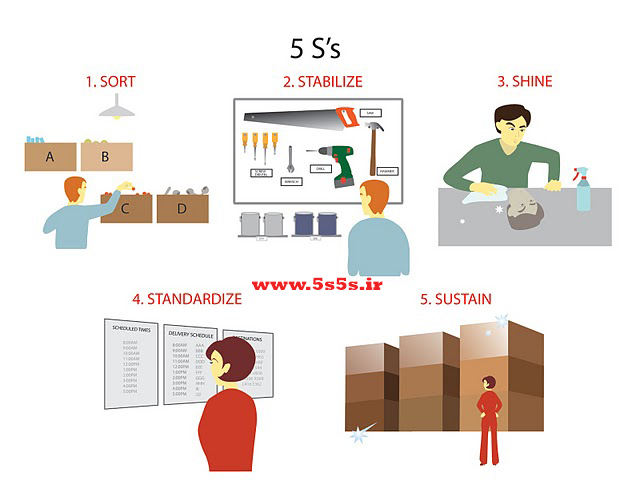
نحوه اجرای سیستم پنجاس (۵S) در ایران خودرو (دستورالعمل)
فاز اول اجرا و استقرار سیستم پنجاس شامل ۳ مرحله بود که تا شش ماهه اول سال ۱۳۷۷ به طول انجامید. مراحل از این قرارند:
- مرحله مقدماتی
- مرحله طراحی و استقرار سیستم
- مرحله تحول سیستم که تا امروز ادامه دارد و خواهد داشت.
در این مراحل نحوه اجرای عملیات و انتقال آن از سطوح عالی و میانی به سطوح اجرای صورت گرفته و مسؤلیت اجرایی هم با رؤسای کل ادارات و کارشناسان بوده است. این افراد به دلیل کثرت مسؤلیت و وظایف و تعداد افراد تحت سرپرستی خود، قادر نبودند. با تک تک افراد بحث کنند و نظارت مستقیم روی عملکرد آنها داشته و سیستم را نهادینه سازند. به همین جهت پس از مدتی به تدریج احساس شد که سیستم وارد دور تسلسل شده و معنا و مفهوم واقعی خود را که ایجاد محیط آرام و با نظم و ترتیب و دور از تشنجات عصبی، روحی و دستیابی به اهدف عالی جهت افزایش کیفیت، کاهش هزینه و جلوگیری از اتلاف منابع میباشد، از دست دادن است.این مسائل در صورتی نهادینه میشود که جزئی از فرهنگ سازمانی باشد و این میسر نیست جز با اهتمام و همیاری همه سطوح اجرایی، میانی و عالی. به همین جهت برای رفع روزمرگی به بهبود مستمر وکایزن کوتاه مدت پرداخته شد و پرداخت پاداش تولید، کارانه و آکورد کارکنان هم بسته به میزان رعایت قوانین آن گردید. امروزه سیستم پنجاس در تلفیق با کایزن در ایران خودرو اجرا میشود.
برای انجام عملیات ۵S یک سالن به دلایل مختلف من جمله وجود محدودههای مشخص به حوزههای سرپرستی تقسیم میشود. سرپرستان به عنوان کلیدهای موفقیت در سازمان شناخته شدهاند و موفقیت نظام مدیریت نویت نسبت مستقیمی با میزان مشارکت سرپرستان در اجرای سیستمها دارد. تقسیم بندی واحدهای مختلف به محدودههای سرپرست و منتقل نمودن مسئولیت اجرایی فعالیتهای ۵S به سطوح اجرایی مطمئناً همکاران سرپرست را فعالتر خواهد کرد.
محدوده سرپرستی (تعریف):
حیطه کاری سرپرست یا استادکار که توسط مهندسی تولید و مدیریت مربوطه مشخص شده و در آن دستگاهها. ماشین آلات و نیروی انسانی مستقر هستند و بخش معینی از محصول را تولید مینمایند.
نتایج حاصل از تعیین محدوده سرپرستی:
- چون مجری و کنترل کننده، خود کارگران و سرپرستها هستند، کار خود را خوب انجام میدهند.
- سرپرست در محدوده کاری خود به جوانب و مشکلات کار مسلط است. بهتر میتواند مشکلات را حل نموده و فعالیتهای خود را بهبود مستمر (علمیات کایزن) دهد.
- با محدود بود افراد شاغل در حیطه سرپرستی آنها میتوانند به راحتی از مشکلات مشخص شده و تا حد امکان رفعشان کنند و با ایجاد ارتباط عاطی به بهبود و تسریع عملیات کمک کنند.
- با کوچک بودن و قابلیت یگیری و شناسای محدودهها، ارزیابی آنها آسان است و زحمات سرپرستان در اجرای ۵S بهتر نمود خواهد داشت و شناسایی و تشوق آنها هم در نتیجه راحتتر است.
- اجرای عملیات بهبود مستمر (کایزن) در حیطههای سرپرستی
هر سرپرست، مسئولترین و متبحرترین فرد ۵S در محدوده سرپرستی خود است و نه با سابقهترین فرد.
نحوه تعیین و شناسایی حوزه سرپرستی:
با توجه به نوع تولیدات و ایستگاههای کاری، محل ورود و خروج کالا، پرسنل ، محل انبار و نگهداری کالا، محل استقرار ماشین آلات و تجیهزات که عامل تعیین کننده محسوب میشوند و پس از چیدمان Lay out محدودههای سرپرستی توسط مهندسی تولید، خط کشی انجام میشود که حوزه سرپرستی (محل مجاز جهت تردد) را مشخص میکند.
کمی راجع به خطکشی (نحوه خطکشی):
انبار قطعات معیوب (سفید، ممتد و پیوسته: انبار کالای در جریان ساخت (سفید، ممتد و پیوسته). محل عبور با احتیاط (پوست پنگی زرد و سیاه و محدوده سرپرستی با خط زرد رنگ ممتد مشخص میشود. خط زرد ممتد پیوسته به عنوان جدا کننده محیط کاری در راهروها. مقطع بهعنوان محل ورود و خروج- محل باز شدن درها و فلش زرد مشخص کننده جهت حرکت در جریان ترافیک است.
سالنهای تولید و محدودههای سرپرستی باید تابلوی مشخص کننده داشته باشند.
سلسله مراتب:
کارخانه سالن تولید خط تولید محدوده سرپرستی ماشین تولیدی
تابلوهای علائم باید بزرگ و خوانا باشد. هر یک از سلسله مراتب فوق رنگ معینی داشته باشد. تابلوهای مهم از محل ورودی باید قابل رؤیت باشد. ماشینهای تولیدی با ذکر کد و نام ماشین روی تابلوها مشخص شوند. در محدوده سرپرستی برگه مشخص کننده مسئول نظافت نصب شود.
ملاحظات در خط کشی محل ورود وخروج کالا و پرسنل:
- توجه به نکات ایمنی
- نشان دادن محل باز شدن درها با خطوط مقطع
- به حداقل رساندن گوشهها
- نشان دادن جهت جریان ترافیک قطعات و کارکنان با فلش زرد رنگ کف سالنها
خط کشیهای محل عبور با احتیاط
برای محل خطرناک با پتانسیل عدم ایمنی از چسب یا رنگ پلنگی سیاه و زرد استفاده میکنیم. به طور مثال موارد زیر قابل ذکر است:
- احتمال وجود شوک الکتریکی
- حفاظ اطراف ماشینها و دستگاههای متحرک و خطرساز
- هر جا که چیزی از دیوار بیرون آمده و میتواند خطرساز باشد.
- محل های با احتمال وقوع حادثه در بالای سر
شناخت و حذف ایرادات ناشی از عوامل تولید در پیادهسازی اصول ساماندهی محیط کار.
پ) کایزن کوتاه مدت در نظام ۵S (تعریف): روشی که در آن تیم کایزن در طی یک روز[۱] مشکلات ۵S را از طریق برگههای ارزشیابی عوامل تولید شناسایی نموده و موظف است در طی یک هفته به حذف یا برنامهریزی جهت حل آنها اقدام نمایند. ایردادات بلند مدت وارد سیستم هوشین میشوند.
قبل از بکار گیری این سیستم ممیزی (بهبود مستمر) ممیزی ۵S انجام میشد. تفاوتهایی که این دو ممیزی با هم دارند به این شرح است: در ممیزیهای ۵S ممیزی و بازرسی بر اساس تفکیک عوامل و اصول پنجاس انجام میشد و بیشتر در راستای استقرار سیستم کاربرد داشتهاند، ولی در ممیزی کایزن یا بهبود مستمر امتیاز بر اساس عوامل تولید (۴M) اعطا میشود. همچین در ممیزی ۵S چون امتیاز منفی وجود نداشت (کار انجام نشده صفر تا ۱۰٫ کار ناقص ۱۰ تا ۹۰ و کار تکمیل شده ۹۰ تا ۱۰۰ امتیاز ) مجموع امتیازات مثبت بود. وی در ممیزی کایزن. چون با دید منفی و کشف ایراد پیش میرویم. مجموع امتیازات منفی است و همه برای کاهش آن تلاش خواهند کرد تا افزاش پاداش برای آنها به ارمغان بیاورد. بعلاوه در ممیزی ۵S تیم تعریف نشده بود.
در راستای اصل نظم و ترتیب از اطول عملیات پنجاس، استاندارد تعیین رنگ تابلوهای شناسایی در ایران خودرو تدوین شده است که نحوه رنگآمیزی تابلوهای مشخص کننده را معلوم مینمایند.
- کارخانه: تابلو با رنگ زمینه قرمز و حروف سفید رنگ کارخانهسواریسازی
- سالن تولید: تابلو با رنگ زمینه سبز و حروف سفید رنگ سالن تزئینات
- خط تولید: تابلو با رنگ زمینه سفید و حروف مشکی خط تکمیل کاری
- محدوده سرپرستی: تابلو با رنگ زمینه زرد و حروف سرمهای ایستگاه شارژگاز
- محل استقرار ماشین آلات : تابلو با رنگ زمینه سرمهای و حروف سفید رنگ ماشین تزریق گاز کولر
تعریف موارد فوق چنین است:
کارخانه: مجموعه سالنهای تولید مختلف ولی مرتبط با هم
سالن تولید: یک زیر مجموعه کارخانه متشکل از تعدادی خط تولید
خط تولید: مجموعهی از دستگاهها. ماشینآلات و نیروی انسانی مرتبط با هم که در یک امتداد به تولید قسمتی از کالای نهایی مشغولند.
محدوده سرپرستی(ایستگاه): حیطه کاری سرپرست که در آن ابزار، ماشینآلات و تجهیزات و نیروی انسانی مستقر شده و مشغول به کار بوده، واحد مشخصی از محصول را تولید میکنند.
ماشینآلات: وسایل تولید مشخصی از محصول که اصل (عدم جابجایی) شامل حال آنهاست.
[۱] کایزن یک روزه در حال حاضر به کایزن کوتاه مدت اصلاح شده است. (بهینهسازی و اصلاح سیستم)