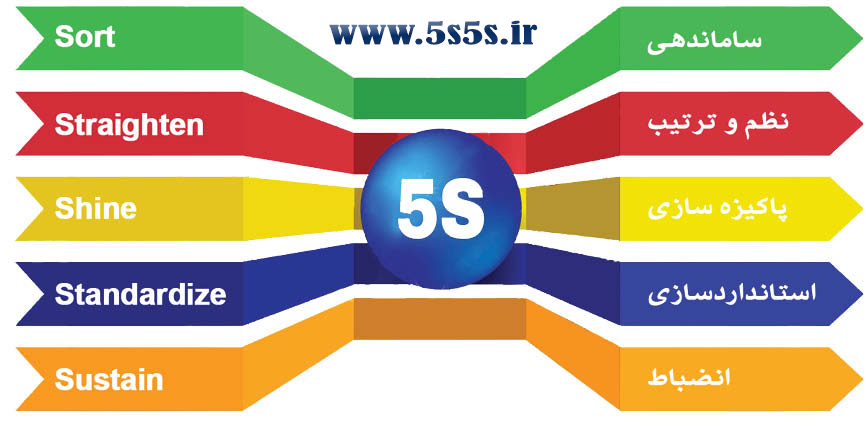
جایگاه ۵S در مدلهای کیفیت و بهرهوری
جایگاه درست و دقیق ۵S
برای توسعه مفهومی و اجرایی کیفیت و بهرهوری در ژاپن برنامه زیر توسعه یافت این برنامهها به صورت وسیعی با یکدیگر ادغام شده و در صنایع ژاپن به کار گرفته شدهاند.
- ۵s (تکلیف، ترتیب، تمیزی، تداوم، تعلیم)
- SS (سیستم پیشنهادات کایزن)
- QCC (حلقه های کنترل کیفیت)
- TQC (کنترل کیفیت فراگیر)
- TPM (نگهداری بهره ور فراگیر)
- JIT (تولید به موقع)
همانطور که معلوم است برنامهها و سیستمهای متعددی نیاز است تا یک سازمان بتواند به سطح مطلوبی از کیفیت و بهرهوری دست یابد. اما نکته بسیار مهم این است که این سیستمها هنگامی اثر بخش بوده و کارآیی خواهند داشت که هر یک از آنها در جای خود به نحو مطلوبی به کار گرفته شوند تا پیاده سازی این سیستمها بر اساس تجارب پیاده سازی آنها در سازمانهای گوناگون میباشد.
اخیراً مشاورین مدیریت همگی همصدا شده و بیان میدارند که ۵S نقطه شروع است و میبایست پیش از TQC، TPM، JIT به کار گرفته شود.ویژگی منحصر به فرد ۵S در این شش برنامه این است که نه تنها مانند تمامی این برنامهها کاربرد سازمانی و جمعی دارد بلکه قابل پیاده سازی در سطح فردی و منزل مسکونی نیز میباشد.
دلایل تقدم اجرای ۵S
همانطور که بیان شد طبق نظر بسیاری از صاحب نظران کیفیت و بهرهوری اجرای۵S پیش شرط اجرای موفقیت آمیز سایر سیستمها و مدلهای مربوطه میباشد از دلایل ضرورت تقدم اجرای۵S میتوان موارد زیر را نام برد:
- اجرای۵S نسبت به سایر سیستمها تا حدودی آسان تر است.
- همه یک محیط کار منظم و تمیز را دوست دارند.
- نتایج حاصل از آن برای همه قابل مشاهده است.
- در همه جا قابل پیاده سازی است.
- سرعت دستیابی افزایش مییابد.
- زمان جستجو به دنبال اشیا و اسناد کاهش مییابد.
- عمر ماشین آلات و تجهیزات افزایش مییابد.
- سلامتی و ایمنی برای کارکنان در محیط کار ایجاد میشود.
- تعداد خطاها کاهش مییابد.
- همه به طور اتوماتیک منضبط میشوند.
- هزینه پیاده سازی خیلی کم است.
- موجب رشد قد را بدانیم و به مشتریان میشود.
- موجب رشد خلاقیت کارکنان برای انجام بهتر کارها میشود.
- موجب بهبود دیدگاه دیگران نسبت به سازمان میشود.
- هر کس میتواند به محل کار افتخار کند.
- عملکرد عمومی سازمان افزایش مییابد.
- جو مساعد برای به کارگیری۵S وجود دارد.
به طور کلی می توان گفت که با اجرای۵S شرایط عمومی سازمان برای ایجاد حداقلهای ضروری مشخص شده و به این ترتیب مدیران سازمان کار کنند میدانند که در چه شرایطی و برای چه هدفی اقداماتی بعدی را انجام دهند.
آشنایی مختصر با TMP
TMP نوعی نگهداری و تعمیرات بهره ور است که توسط کلیه کارکنان به صورت فعالیتهای گروهی در گروههای کوچک اعمال میشود. به طریقی مشابهTQC که نوعی کنترل کیفیت جامع در سطح کل شرکت است. TMP نیز نوعی برنامه برای نگهداری و تعمیرات تجهیزات کارخانه با همکاری کل کارکنان شرکت میباشد واژه نگهداری و تعمیرات بهره ور جامع (TMP) در سال ۱۹۷۱ توسط موسسه مدیران فنی ژاپنی که قبلا موسسه نگهداری و تعمیرات ژاپن نامیده میشد با پنج هدف اصلی زیر تعریف شده است:
- حداکثر نمودن اثربخشی تجهیزات(بهبود راندمان کل)
- توسعه دادن یک بسته نت بهره ور برای کل دوره عمر تجهیزات
- درگیر نمودن کلیه بخشهای صنعت که به امور برنامه ریزی طراحی بهره برداری و نگهداری و تعمیرات دستگاه ها می پردازند در امورTMP(مهندسی و طراحی تولید نگهداری و تعمیر)
- درگیر نمودن فعالانه کلیه کارکنان از مدیریت رده اول تا کارگران سطح کارگاه
- توسعه دادن TMP از طریق مدیریت انگیزهای، فعالیت های گروههای کوچک خود ساخته و مستقل
کلمه Total (فراگیر) در عبارت نت بهره ور فراگیر سه مفهوم اساسی را در ارتباط با سه ویژگی مهم TMP موارد زیر را در بر میگیرد:
اثربخشی فراگیر: توسعه و بهبود راندمان اقتصادی یا سودمندی
پیشگیری فراگیر: طراحی دستگاههای بی نیاز از تعمیر و همچنین تعمیرات پیشگیری جامع
همکاری و اشتراک مساعی فراگیر: انجام عملیات نگهداری و تعمیرات به صورت خودساخته و مستقل توسط کارگران بهره برداری در گروه های کوچک در هر یک از بخشهای صنعت و همچنین توسط سایر سطوح کارکنان به صورت مشابه.
در ژاپن از “۵S” به عنوان اصول پایه و بنیادی صیانت صنعتی یاد میشود. در موارد زیادی اصول “۵S” به صورت ظاهری و تشریفاتی مورد توجه قرار میگیرند.(مثال: رنگ آمیزی کف کارگاه و بدنه ماشین آلات)
در حالی که در امور اساسی مورد نیاز و تعبیر نظیر قسمتهای داخلی دستگاه و قسمتهای دوال به فراموشی سپرده میشود. اینگونه عملیات ظاهری و زرق و برقدار در نظام TMP حذف میشوند دلیل این امر این است که برنامههای آموزشی پرسنل شامل کارآموزیها و تجربههای آموزشی در حین کار به هفت مرحله تقسیم میگردند که یکی از این مرحله اعمال اصول ۵S است. در این برنامههای آموزشی باید کاراموزان به مسئولیتها و وظایف مربوط به هر مرحله آگاهی و تسلط کامل پیدا کنند تا امکان آغاز مرحله بعدی برای آنان فراهم گردد.
اصول ۵S بهبود عملیات آماده سازی نیز نقش بسزایی دارد در بهبود عملیات آماده سازی و تنظیم باید قانون ساده را همواره در نظر داشت:
- به دنبال قطعات ابزار نگردید.
- حرکات غیر ضروری ننماید میز کار را به صورت مناسب قرار دهید و محلهای نگهداری را نیز به نحو مناسب تعیین کنید.
- از ابزار و قطعات نامناسب استفاده نکنید.
در عملیات آمادهسازی اصول ۵S باعث راهنمایی افراد میشوند تا افراد بدانند چگونه پیشبینی و آمادگی را در حالی که ماشین در حال کار است باید انجام دهند تا مطمئن باشند که هرگاه به هر گونه قطعه یا ابزاری نیاز داشتند به تعداد لازم برایشان آماده است. کارگران از اصول نظم و ترتیب استفاده مینمایند تا اطمینان داشته باشند که استانداردها را پیگیری نمودهاند و کیفیت و بهرهوری را در پیش دارند. برای مثال لیستی از عملیات لازم تهیه کردهاند روی تابلوهایی نصب آچارها و ابزارها یک نوع سیستم کنترل عینی طراحی نمودهاند و همین کار را در مورد جعبههای قطعات نیز انجام دادهاند و محل استقرار میز کار و نظایر اینها را به خوبی تعیین نمودهاند.
اصول سازماندهی نظم و پاکیزگی شامل توجه نمودن و رعایت نمودن دقیق استانداردها است. این اصول عمدتاً با مسئولیتهای اپراتورها مرتبط میشود. با توجه به اینکه باید اپراتورها در رعایت استانداردها کوشش نمایند بنابراین فعالیتهای گروهها به مسائلی نظیر دستیابی به راه حل سادهتر برای پیروزی از استانداردها، نظیر استفاده خلاق از حواس انسانی متمرکز میشود. بنابراین سازماندهی و نظم و پاکیزگی عبارت است از فعالیتهای توسعه و تکامل به منظور سادهسازی و استاندارد نمودن عواملی که باید تحت کنترل و نظارت قرار گیرند و همچنین شامل دستیابی به راه حلهای خلاق برای اطمینان از رعایت استانداردهای مدون هستند. در این راستا مدیران و کارگران دست به دست هم دادند و سعی دارند که برایشان اطمینان حاصل شود که عامل استانداردسازی و کیفیت و بهرهوری و کنترل چشمی به صورت فراگیر در سطح کارخانه اعمال میشود.
منبع: کتاب ساماندهی محیط کار و منزل بر اساس سیستم ۵S
نویسنده: ناصر صادقی فرد